Whether on a construction site or an industrial production line, the choice of fasteners is one of the important factors that determine the quality of the project. A small screw may take on the stability of the entire system. Therefore, the selection of suitable and reliable fasteners becomes particularly important.
Today we will focus on a highly respected solution-the 2BA extension screw. This precision manufactured parts not only have excellent strength performance, but also meet the high standards of long-term use in complex environments.
First, let's take a look at what makes it unique? First of all, the material is made of high quality stainless steel, which has strong corrosion resistance and high temperature resistance. Secondly, after special process treatment, the surface is smooth and flawless and has self-lubricating function to reduce the wear probability and greatly improve the service life. In addition, it is specially designed into a fine tooth structure to make the locking force greater and more stable, especially suitable for those occasions that require frequent disassembly but need to maintain good sealing performance, such as pipe flange connection.
Because of these unparalleled advantages, this product is widely used in many fields, including but not limited to aerospace equipment assembly, offshore oil platform construction, and automobile manufacturing. Every industry has its own unique challenges and this versatile and adaptable tool is designed to meet the demands of a wide range of demanding tasks.
In order to give you a better understanding of its practical utility, let's illustrate the problem with a specific example. In the early stage of a large bridge construction project, the loosening of some components seriously affected the overall progress and even threatened the safety of life and property of personnel because the traditional common model could not withstand the huge pulling force. Later, the technicians were decisively replaced by a stronger and firmer new generation of 2BA series. After all hidden dangers were solved, the acceptance work was successfully completed and unanimously praised.
Of course, the correct method of operation is also one of the prerequisites for full potential. It is suggested to determine the diameter of the drill hole first, then gently screw it into several circles by hand to confirm the accurate position, and then gradually increase the torque with the help of a professional electric wrench until it reaches the predetermined value. Do not use too much force at one time to avoid damage and backfire.
In addition to the above mentioned content outside the regular cleaning and maintenance of the same can not be ignored. At ordinary times, attention should be paid to prevent dust and impurities from entering the gap and affecting normal operation. If signs of rust are found, timely application of anti-rust oil for protective treatment can significantly delay the aging speed so that the whole system can always maintain the best state of operation.
Finally, looking to the future, we can foresee that with the continuous progress of science and technology, new materials and new design concepts will surely promote the entire fastener industry to a higher level. At that time, there may be more innovative products to break through the existing limitations and bring us more surprises. Looking forward to the early arrival of that day!
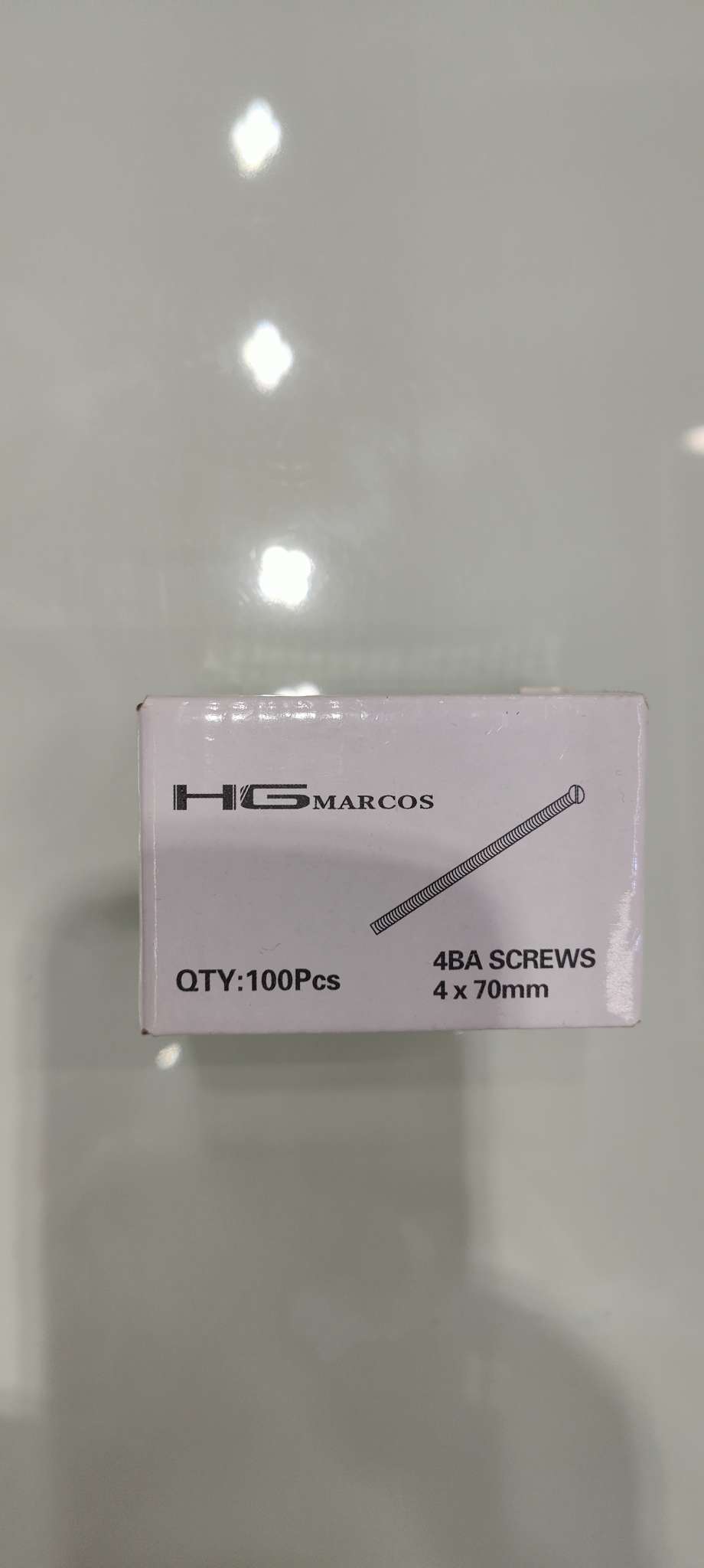